El mantenimiento predictivo es una técnica más dentro de las posibles para elaborar un plan de mantenimiento en una planta industrial y que presenta algunas ventajas importantes sobre otras técnicas.

El objetivo fundamental de la implantación de un programa de mantenimiento predictivo en una planta industrial es aumentar la disponibilidad y disminuir costes de mantenimiento. El análisis de una planta industrial según esta metodología aporta una serie de resultados:
- Mejora la comprensión del funcionamiento de los equipos y sistemas.
- Analiza todas las posibilidades de fallo de un sistema y desarrolla mecanismos que tratan de evitarlos, ya sean producidos por causas intrínsecas al propio equipo o por actos personales.
- Determina una serie de acciones que permiten garantizar una alta disponibilidad de la planta.
¿Cuándo fallara? ¿Cómo evito paros no programados?
Aunque es virtualmente imposible determinar cuándo fallara una maquinaria crítica para su planta, si es posible anticiparse a fallas con un buen programa de mantenimiento y el buen uso de las herramientas adecuadas. La frase “el que no mide no conoce” es muy aplicable al mantenimiento industrial, puesto que es una parte importante de ello. Para poder anticiparse a fallas, el monitoreo de parámetros mediante la medición es crucial.
Pero las interrogantes son ¿Cómo medimos? ¿Con que medimos?
Termografía
El calor suele ser un síntoma temprano de daños o funcionamiento incorrecto en el equipo, el cual lo convierte en un parámetro clave del rendimiento controlado en los programas de mantenimiento predictivo. La correcta utilización de termo-cámaras y una buena interpretación de una imagen térmica es parte esencial del mantenimiento predictivo.
Con el análisis de imágenes térmicas se pueden detectar posibles anomalías a través de patrones térmicos. Las termo-cámaras, le permiten ver situaciones que a simple vista no se pueden ver con el ojo humano. Esta visualización ofrece una ventaja para tomar decisiones sobre maquinaria que su paro represente un alto impacto económico.
Calidad de la energía.
Las instalaciones eléctricas usualmente son comprobadas al momento de la construcción de la planta y muy comúnmente no se vuelven a verificar. Esto es porque “aparentemente” no existe falla alguna y se crea la impresión de que todo funciona de maravilla. Sin embargo la realidad es distinta cuando alguna maquinaria falla sin razón aparente, el recibo de energía se comienza a elevar o tenemos una multa por bajo factor de potencia.
Las perturbaciones eléctricas siempre están presentes en una instalación eléctrica industrial. Se definen en términos de magnitud y duración.
Estas perturbaciones varían desde microsegundos a cortes del servicio eléctrico que se prolongan durante horas. Una perturbación eléctrica hace que el suministro supere los límites de operación y que la maquinaria instalada funcione de forma incorrecta o incluso la dañen.
El mantenimiento predictivo aplicado a la calidad de la energía involucra el uso de herramientas adecuadas para el correcto monitoreo de la instalación eléctrica.
Con el objetivo de mejorar la eficiencia eléctrica y con ello reducir el consumo, alargar la vida de la maquinaria eléctrica y evitar paros no programados.
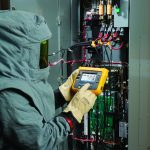

Vibración.
La vibración sigue siendo uno de los indicadores más prematuros de la “salud” de una máquina. Sin embargo el tema de análisis de vibraciones puede ser algo extenso y requiere un grado alto de conocimiento para poder entenderlo. El análisis de vibraciones tradicional implica instrumentos que, debido a su complejidad técnica especialmente en el diagnóstico de las gráficas espectrales, no está al alcance de todos.
Afortunadamente gracias a los avances tecnológicos existen herramientas especializadas para el mantenimiento industrial que le ayudan a rápidamente diagnosticar posibles problemas a través del análisis de vibración. Estas herramientas le permiten:
Conocer de forma rápida y fiable “la salud” de la maquinaria y la gravedad de su estado.
Aumentar la eficiencia trabajando con una lista priorizada de problemas.
Tomar el control de los costos derivados del tiempo de inactividad mediante la anticipación a los problemas con mayor premura y la identificación de las causas que originan las fallas más recurrentes.
Aumentar el nivel de eficiencia del departamento de mantenimiento.
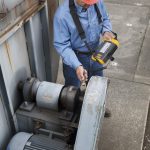
Resistencia de Aislamiento.
La comprobación de la resistencia de aislamiento en maquinaria instalada en la planta, también es parte del mantenimiento predictivo.
La mayoría de las instalaciones necesitan aprovechar al máximo sus motores ya que su sustitución representa un gran esfuerzo, no sólo económico sino también físico. Las mediciones eléctricas, de resistencia de aislamiento y térmicas son tres pruebas que pueden ayudar a solucionar los problemas de los motores, variadores y circuitos eléctricos asociados, así como a prolongar su ciclo de vida operativo.
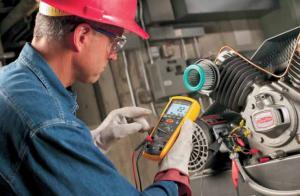
Se recomienda un programa regular para probar la resistencia de aislamiento, para prevenir descargas eléctricas, asegurar la seguridad del personal y reducir o para eliminar tiempos muertos. Detectar el deterioro de aislamiento ayuda a programar anticipadamente el trabajo de reparación. También es provechoso para la evaluación de la calidad de las reparaciones antes de poner el equipo nuevamente en funcionamiento.
No hay una regla rápida e indiscutible para interpretar los valores de resistencia de aislamiento, pero los fabricantes y agencias, sí parecen estar de acuerdo en que la tendencia del valor de aislamiento puede ser un claro indicador de la futura “salud” de un motor.
Alineación de motores por medio de Laser
Parte de un buen plan de mantenimiento a motores deberá de incluir una verificación y corrección constante en la alineación de ejes.
Si bien un analizador de vibraciones podrá determinar si existe una vibración severa por mala alineación. Se debe contar con las herramientas adecuadas para realizar una correcta alineación del motor con sus acoplamientos.
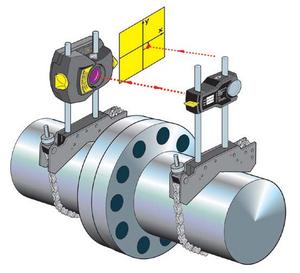
Es un hecho conocido que todo motor o maquinaria giratoria es susceptible a desalineaciones. Si todavía utiliza reglas e indicadores de cuadrante para asegurarse de que su maquinaria giratoria se encuentra adecuadamente alineada, es posible que esté perdiendo miles de dólares por año en costos de rodamientos de reemplazo, horas innecesarias de reparación y tiempo fuera de servicio no planeado, sin considerar la disminución en la vida útil de su maquinaria.
Utilizando herramienta de alineación de ejes por láser le proporciona de manera rápida y precisa respuestas prácticas que mantendrán su planta en funcionamiento. Estas herramientas realizan los cálculos de alineación complicados por usted, lo que significa que obtendrá las respuestas que necesita para alinear en forma rápida su máquina.
En esencia el Mantenimiento Predictivo consiste en la realización de constantes mediciones en la maquinaria de planta; esto incluye equipos, herramientas, sistemas etc.
Con el fin de predecir alguna falla futura con una ventana de tiempo para hacer cambios y tomar decisiones con mucha mayor confianza. El mantenimiento predictivo es la ruta a seguir para evitar dolores de cabeza innecesarios. Sobre todo si está cansado de “apagar fuegos” y corregir problemas bajo presión por paros no programados.